Non-Destructive Testing Applications in Various Industries
Non-destructive testing (NDT) has emerged as a cornerstone technology in diverse industries, safeguarding structural integrity while optimizing operational efficiency. From aerospace to construction, from manufacturing to energy, NDT's versatile applications have redefined the way we ensure quality and safety in critical components.
NDT Applications Enhance Fastener Quality and Reliability in the Fastener Industry
Fasteners form the backbone of countless applications, from automotive and construction to aerospace and manufacturing. Ensuring the integrity of these connections is critical for safety and performance. Explore how non-destructive testing technology is revolutionizing the assessment of fastener applications, guaranteeing their quality without compromising structural strength. Fasteners serve as the linchpin in assemblies, and their failure can lead to catastrophic consequences. From vibration-induced loosening to material defects, identifying potential weaknesses is crucial. NDT steps in as a reliable solution to uncover hidden problems, ensuring fastener reliability in demanding environments.
Bearing Industry: Ensuring Precision and Reliability in Mechanical Systems with Bearings Through the Application of NDT
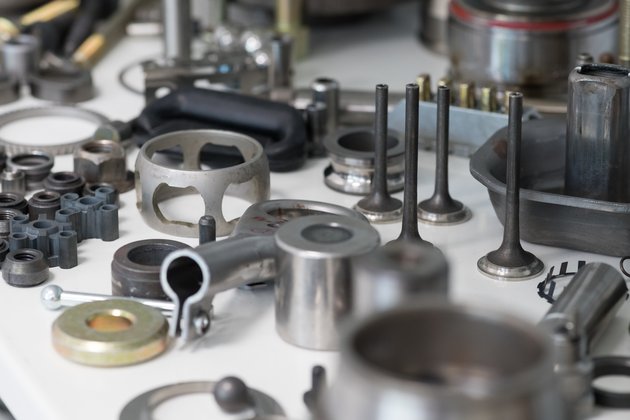
Bearings are the unsung heroes of countless mechanical systems, enabling smooth motion and reducing friction. In the dynamic world of bearings, non-destructive testing emerges as a pivotal technology, ensuring that bearings meet exacting standards of quality, performance, and safety across diverse applications.
From industrial machinery to automotive vehicles, bearings are integral to the functionality of mechanical systems. A faulty bearing can lead to increased friction, reduced efficiency, and even catastrophic failure. NDT technology steps in as a guardian of precision, detecting imperfections that might otherwise go unnoticed.
Non-Destructive Testing Applications in the Automotive Industry Ensure Vehicle Safety and Longevity
In the automotive industry, NDT guarantees the safety of vehicles on the road. It ensures the integrity of materials used in manufacturing, detects flaws in welds and joints, and identifies potential weaknesses in safety-critical components. NDT not only enhances road safety but also contributes to the longevity of vehicles.
Wind Energy: Increasing the Performance and Reliability of Wind Turbines in Renewable Energy with Non-Destructive Testing
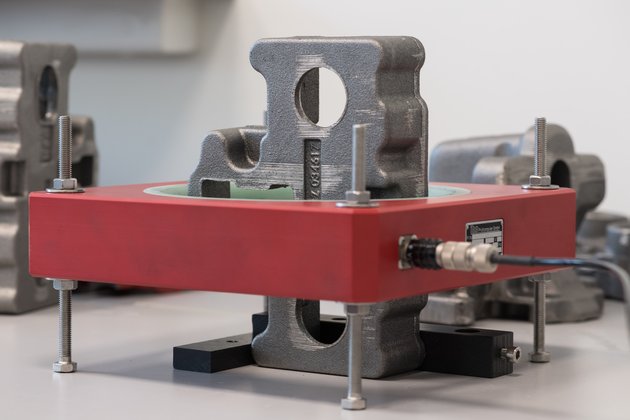
Wind energy stands at the forefront of sustainable power generation, and wind turbines play a pivotal role in converting wind into electricity. Ensuring the reliability, safety, and longevity of these complex structures is paramount. Non-destructive testing emerges as a driving force in the wind energy sector, enhancing turbine performance and contributing to the growth of renewable energy.
Wind turbines are exposed to harsh environmental conditions, from extreme winds to temperature fluctuations. Ensuring their structural integrity is critical for safe and efficient energy production. NDT technology allows minimizing downtime and reducing maintenance costs.
Aviation and Aerospace Industry: Precision Assurance in Aerospace with NDT Testing Applications
In aviation and aerospace, precision is paramount. NDT plays a pivotal role in detecting hidden defects in aircraft components, engine parts, and even aerospace structures. Through methods like eddy current testing, NDT ensures that every part meets rigorous standards, minimizing risks and upholding airworthiness.
NDT in Healthcare: Ensuring the Quality Standards of Medical Devices
Even in healthcare, NDT plays a role. Medical devices, from implants to diagnostic equipment, undergo NDT to ensure they meet stringent quality standards. This ensures patient safety and the effectiveness of medical interventions, leaving no room for compromise.
Enhancing Precision and Product Reliability through Non-Destructive Testing Applications in Manufacturing
In manufacturing, NDT technology is a game-changer. It ensures that products meet exact specifications without compromising on quality. By inspecting materials, welds, castings, and machined parts, NDT identifies flaws that could impact performance. This leads to improved product reliability and reduced rework costs, ultimately enhancing customer satisfaction.
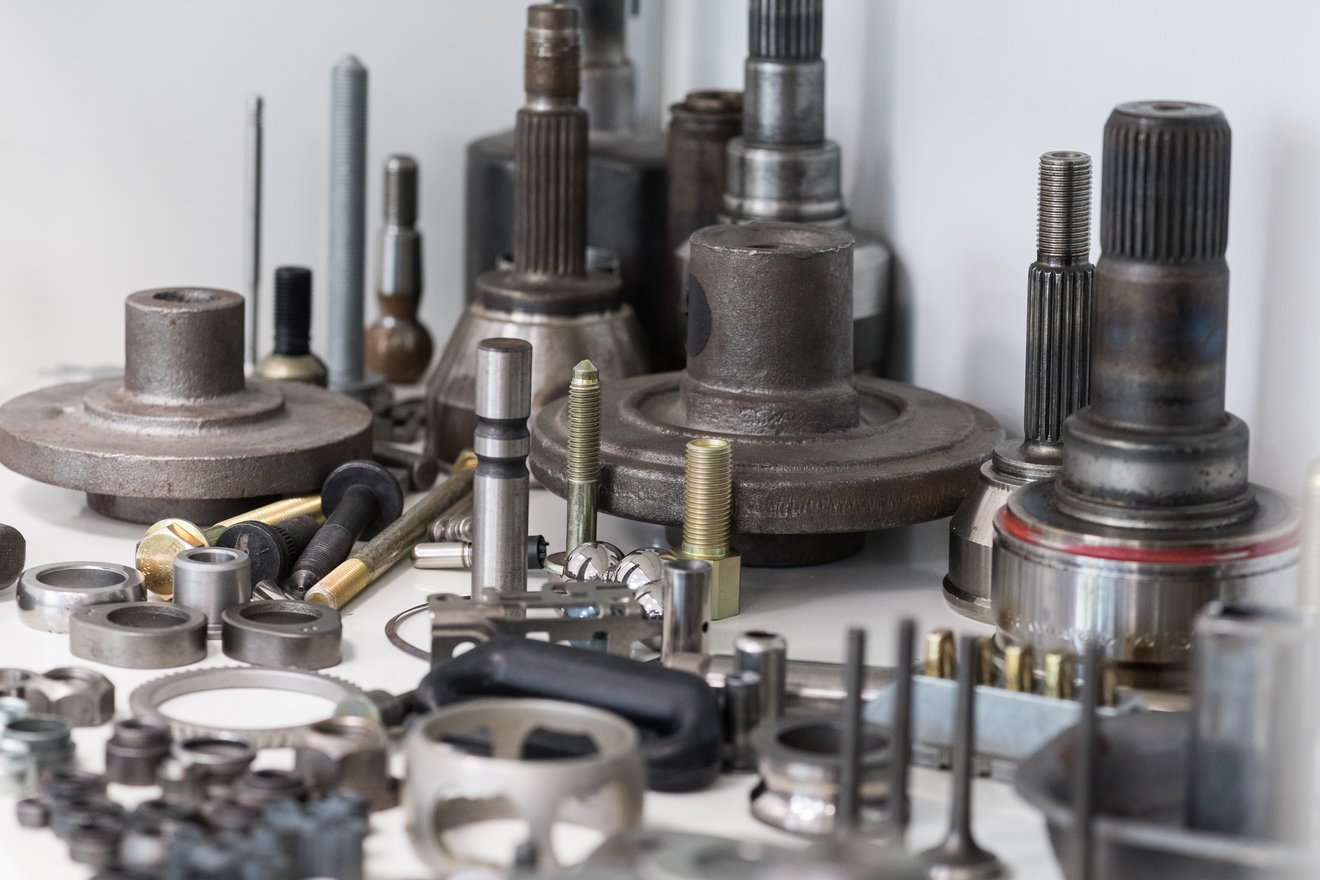
The Future of NDT
As industries evolve, so does NDT technology. Advanced techniques with the future help of Artificial Intelligence evaluation continue to push the boundaries of what NDT can achieve. Regardless of the application, NDT remains a steadfast guardian of safety, quality, and efficiency, ensuring that the products and infrastructure that shape our world stand the test of time. Contact us today to learn more about how NDT can revolutionize quality assurance and safety in your industry.
Contact Us